Project Overview
A prominent steel distributor in Australia, known for supplying sheet and coil products nationwide, faced challenges in safely transporting rolled steel items. These products, due to their smooth surfaces and substantial weight, posed significant risks during transit, especially when placed directly on steel truck decks. The inherent slipperiness of steel-on-steel contact made it imperative to find a solution that would ensure compliance with safety regulations and protect the integrity of the cargo.
Challenge
Transporting rolled steel coils requires meticulous attention to load restraint to prevent movement that could lead to accidents or product damage. The National Transport Commission’s Load Restraint Guide 2018 emphasizes the importance of preventing
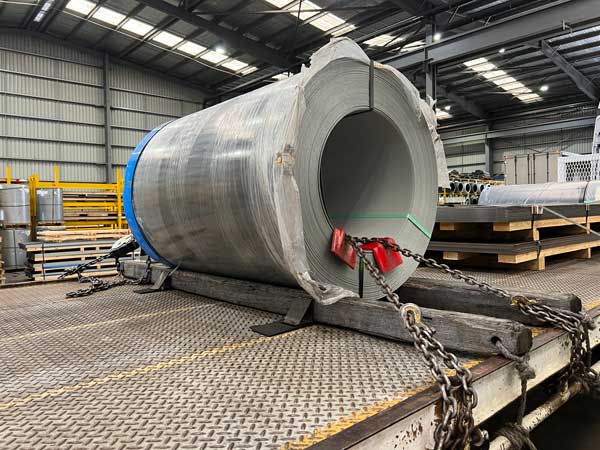
load movement in all directions during normal driving conditions, including acceleration, braking, and cornering. Traditional methods, such as using timber dunnage and steel support frames secured with chains, were standard practice. However, these methods alone were insufficient in preventing the steel frames from slipping on the truck decks, especially under dynamic driving conditions.
Solution: Implementation of Durable Rubber Load Mats
To address this issue, the distributor incorporated heavy-duty Reglin Rubber load mats beneath the steel support frames. These anti-slip rubber mats significantly increased the friction between the frames and the truck deck, effectively minimizing the risk of slippage. Unlike previous recycled rubber mats, which tended to degrade and break apart under the stress of heavy loads and repeated use, the newly adopted solid rubber mats demonstrated exceptional durability. They withstood the rigors of transporting heavy steel coils across long distances without showing signs of wear or compromising their friction-enhancing properties.
Outcome
The integration of Reglin Rubber load mats into the load restraint system yielded several benefits:
- Enhanced Safety: The increased friction provided by the rubber mats ensured that the steel support frames remained securely in place during transit, reducing the risk of accidents caused by load shifts.
- Regulatory Compliance: By preventing steel-on-steel contact and adhering to the guidelines set forth in the Load Restraint Guide 2018, the distributor maintained compliance with national safety standards.
- Cost Efficiency: The longevity of the solid rubber mats meant fewer replacements and maintenance interventions, leading to cost savings over time.
- Operational Efficiency: With a more reliable load restraint system, the distributor experienced fewer delays and disruptions, ensuring timely deliveries to customers across the country.
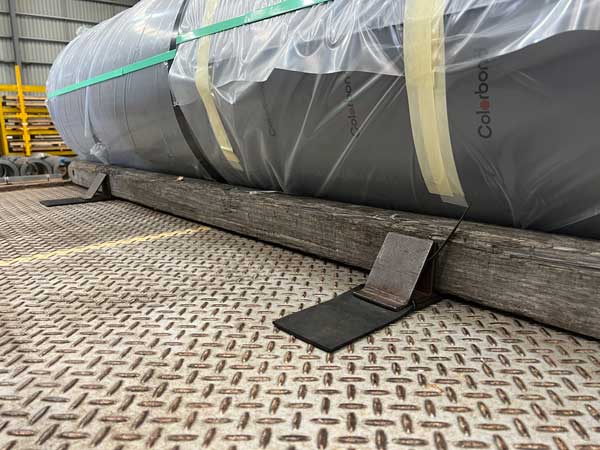
Conclusion
The adoption of Rubber Rubber load mats proved to be a pivotal enhancement in the transportation of rolled steel products. By addressing the critical issue of load slippage, the distributor not only ensured the safety of their operations but also achieved greater efficiency and compliance with national transport regulations. This case underscores the importance of continually assessing and upgrading load restraint systems to meet the evolving demands of heavy-duty transport logistics.