Project Scope
Supply of rubber bearing strips for use between precast concrete components in marine construction
Product
Reglin Neoprene HG Rubber Strip
Size: 3mm thick x 200mm wide
Supplied: Over 1,000 L/M of cut strips
Project Overview
A major marine infrastructure upgrade was undertaken at an operational wharf facility in NSW, Australia. As part of the construction process, a specialist marine construction contractor was engaged to install a large number of precast concrete headstocks and crossbeams as part of the new wharf structure.
These elements were to be installed in a challenging marine environment where the long-term performance of materials was critical. Due to exposure to saltwater, UV radiation, and wide temperature fluctuations, the project design team needed materials that could withstand these harsh conditions while maintaining their structural integrity and performance.
Challenge
Precast concrete elements in marine construction must be installed with precision and supported in a way that accommodates:
- High compressive loads from the structure above
- Tolerances between sections during installation
- Thermal movement and vibration
- Prevention of edge spalling or cracking over time
- Environmental durability in a coastal setting
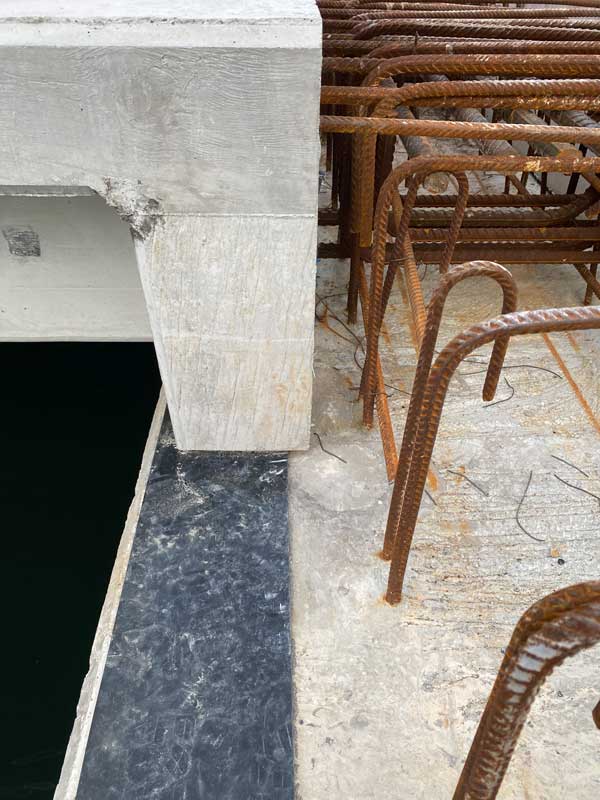
Without the right interface material, differential loading and uneven pressure points could damage the concrete sections, reduce service life, and lead to future maintenance or structural concerns.
Solution: Neoprene HG Rubber bearing strips installed between precast concrete sections.
To address these challenges, the contractor selected Reglin Neoprene HG Rubber Strips as the ideal material to be placed between precast components.
Manufactured from premium-grade chloroprene (Neoprene) rubber, these strips offered a combination of properties that made them highly suitable for marine construction:
- Durability & Resilience: Neoprene rubber maintains flexibility and compressive strength under sustained loads. The 60 durometer hardness balanced structural support with enough cushioning to absorb minor surface irregularities.
- Load Distribution: Installed between the precast concrete beams and piles, the strips helped evenly distribute load, reducing point loading and preventing spalling.
- Movement Accommodation: Their elastic properties allowed for minor thermal movement and vibration dampening from environmental and structural forces.
- Marine Resistance: Neoprene’s inherent resistance to seawater, ozone, and UV ensured long-term durability in the exposed wharf environment.
- Installation Efficiency: Cut in-house to 3mm x 200mm, over 1,000 linear metres of strip were delivered ready for immediate installation, aiding site efficiency and build schedule.
Conclusion
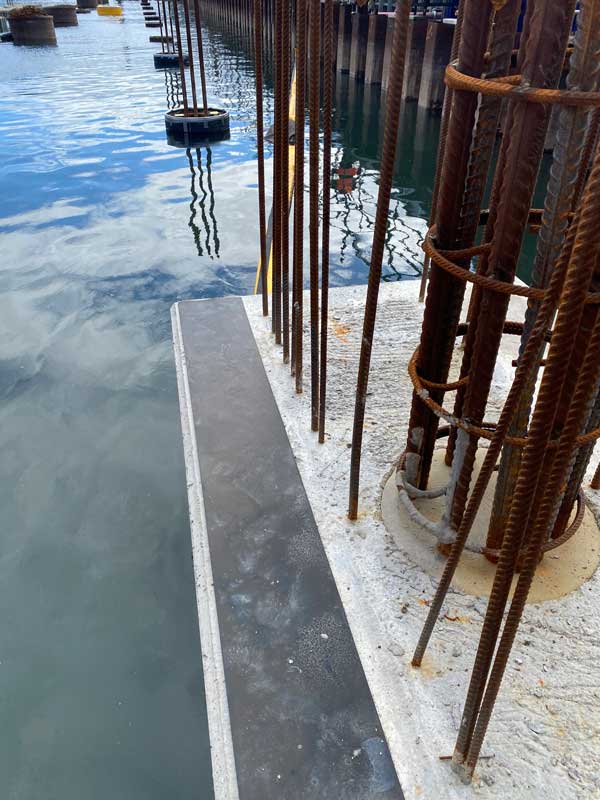
The use of Reglin Neoprene HG Rubber Strips was a critical component of the precast concrete installation method used in this wharf construction project. By providing a durable, weather-resistant and load-bearing interface, these strips supported both the structural performance and long-term service life of the marine infrastructure.
Their success in this project reinforces the importance of selecting the right rubber materials for use in coastal and marine construction environments. Reglin’s ability to provide technical support, quick turnaround, and high-quality rubber products made them a valuable supplier for this critical marine application.